Гумова суміш.
Цех змішування. Тут здійснюється процедура приготування готових сумішей, які йдуть у виробництво. Процес ділиться на два етапи. На першому відбувається змішування безпосередньо гумових сумішей, тобто каучукових складових (натурального і синтетичного). Уже на другому етапі додаються інші «не гумові» компоненти: сажа, силика, всілякі хімічні добавки (їх може бути близько 20 штук), зміст яких різниться в залежності від рецептури суміші. Всі компоненти ретельно зважуються оператором і по конвеєрній стрічці відправляються в спеціальну піч. В середньому, цех змішування виробляє до 800 тонн готової суміші щодня, яка на виході являє собою стрічку нарізану шматками певної довжини.
Наступна ділянка - лінія для корду. Тут сталевий і текстильний корд, проходячи між спеціальними барабанами, заливається гарячою гумової сумішшю, а на виході готова стрічка нарізається шматками необхідної довжини. На цій ділянці здійснюється внутрішній шар шини, текстильний шар, брекерного шари різних типів. Кінцевий продукт надходить на ділянку складання готових компонентів.
Протектор.
До екструдеру за допомогою конвеєра подається стрічка готової суміші, де шнековий механізм проганяє її через шаблон. Після проходження через отвір шаблону змієподібною тіло протектора безперервної стрічкою надходить в охолоджуючий механізм, де також маркується і обробляється спеціальним цементом, після чого протектор нарізається. Контроль довжини забезпечується спеціальним обладнанням. До речі, механізм розрізає стрічку під кутом, щоб потім при складанні шини можна було з'єднати початок і кінець протектора внахлест і уникнути видимих швів.
Боковини.
За тим же принципом виробляються і боковини шини. Точно так само як протектор, стрічка для боковини видавлюється через шаблон за допомогою екструдера. Різниця лише в готових сумішах і в тому, що боковина розрізані, а завивається в спеціальні барабани.
Бортові кільця.
Це своєрідні ребра жорсткості шини. Десяток величезних барабанів крутиться, віддаючи запаси металевого дроту обладнання з виробництва бортових кілець. Дріт складається в пучки необхідної товщини і жорсткості, а потім обрезінівается надходить сумішшю. Одна зміна виробляє близько 3600 бортових кілець.
Процес складання шини складається з двох етапів.
На першому етапі з необхідних компонентів виробляється каркас. Внутрішній шар, текстильний шар, стрічка боковини подаються на складальний верстат, а з боків перераховані вище компоненти замикаються бортовими кільцями. Одночасно підігріваючись і прокручиваясь. Одна зміна виробляє 650 каркасів
Другий етап - остаточне складання шини. На каркас наноситься необхідну кількість брекерних шарів і протекторна стрічка. Цікаво, що брекерного шари і протектор спочатку з'єднуються один з одним, а потім на верстаті автоматично переносяться на готовий каркас, де закаточні ролики допомагають їх закріпити. Тепер шина зібрана і готова до вулканізації.
Вулканізація - завершальний процес у виробництві, який здійснюється в пресах-вулканізаторах. Форма шини, боковини, маркування і, найважливіше - малюнок протектора, наносяться за допомогою сегментних форм, які виробляються тут же, в спеціальному цеху при заводі. Зсередини шини розпирають спеціальні вулканізаційні діафрагми. Процес приготування однієї легкової шини протікає 10-15 хвилин при температурі 170 ° С і тиску в 20 Бар.
Шина готова. Залишається тільки вихідний контроль. Незважаючи на те, що на кожній стадії виготовлення продукту, здійснюється свій контроль, перевірка готового продукту (причому всіх примірників) обов'язкове. Спочатку шини проходять візуальний контроль. Потім за допомогою спеціалізованого обладнання здійснюється перевірка на однорідність і биття шини (радіальне і діагональне). Після цього шини відправляються в склад готової продукції. Якщо на якомусь етапі шина відбракована, то вона надходить на ділянку грейдера. Тут фахівці вирішують, чи можливий ремонт цієї шини. Вона або ремонтується і знову проходить всі етапи перевірки, або відбраковують остаточно і йде в переробку.
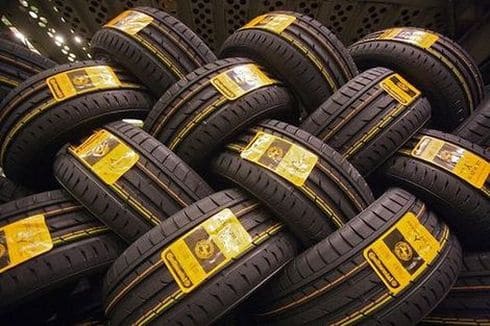